How To Make A Patch Panel
Article by Mark Trotta
If a body panel has rust spots but no collision damage, replacing the whole panel may not be necessary. An alternative is to cut out only the rusted area, then make a template, trace it onto sheet metal, cut it out, and weld it in. This is a time consuming process, but having the right tools will save you time (providing that you use them correctly).
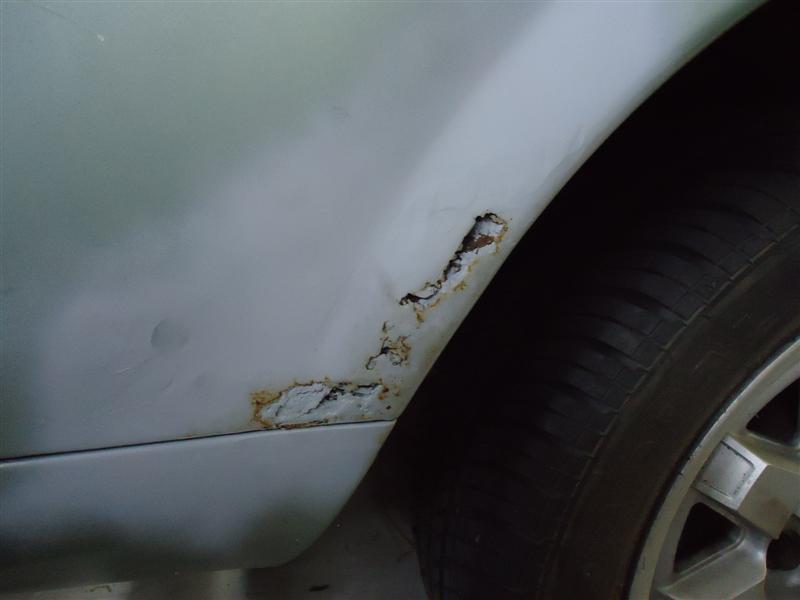
Full Panel vs Patch Panel
If you bring your car to a body shop, they'll want to replace the entire panel, regardless of whether or not it can be repaired. This is simple economics--it's quicker and more cost-effective for them to replace the whole panel. The labor may be less, but overall you'll pay more once you include the cost of the replacement panel. This often puts body repair out of a person's restoration budget.
Provided you are a decent welder, you can save money by cutting out the bad metal, making a patch panel, and welding it in. If you're just getting started with automotive body repair, a MIG Welding Machine is a good choice. It's the easiest welding process to learn and also cheapest to buy. Most people can produce quality, good looking welds with minimal practice.
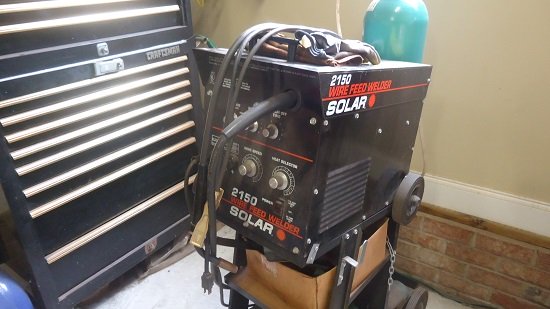
You need to bring the panel down to bare metal. A D/A sander works best for this. An angle grinder with a wire brush attachment can also be used.
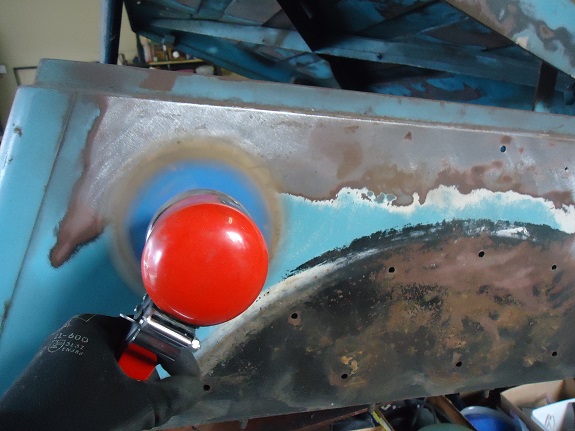
Before cutting out the rusty metal, take a wire brush and/or scraper and remove any loose rust on the body panel to be worked on. Then take masking tape and mark out about one inch beyond the rusted-through part. You want to remove as little good metal as possible.
Cutting and Removing Rusty Panels
Cutting out damaged metal can be done several ways. An air compressor and cut-off wheel is one popular method.

Another way is with an electric angle grinder.
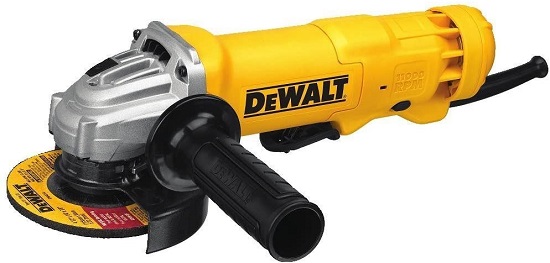
Once the rusted part is cut away, an air sander can be used to bring the area down to bare metal.

Sand beyond the rusted area an inch or so. A 36-grit sanding disc works the fastest. Clean the exposed area with a 60 or 80-grit disc. You should now have a shiny, solid rust-free surface.
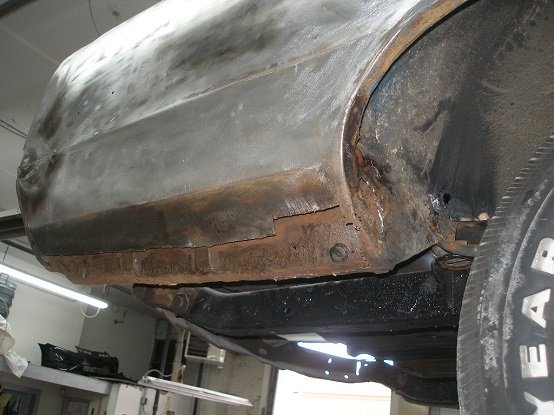
Patch Panel Template
After carefully cutting out all the rust from the panel, the next step is to make a patch template. Take measurements and transfer them to a piece of cardboard (the kind you can cut with a scissor). Draw and cut a template of the patch panel needed.
When cutting sheet metal for a patch panel, start larger than you actually need. You will be trimming it to fit slowly and carefully.
Scribe or mark the cardboard template onto a piece the piece of sheet metal. You can use a black marker to mark the cut, and remember to add about an 1/8th" or so to the line for trimming.
It's easy to remove metal - much more difficult to add it!
Cutting Sheet Metal
Sheet metal can be cut in a number of ways. Hand-held nibblers and tin-snips work fine for smaller patches, but electric shears will save time on larger patches.
Once you have the rough patch cut out, carefully trim it down with hand-held snips.
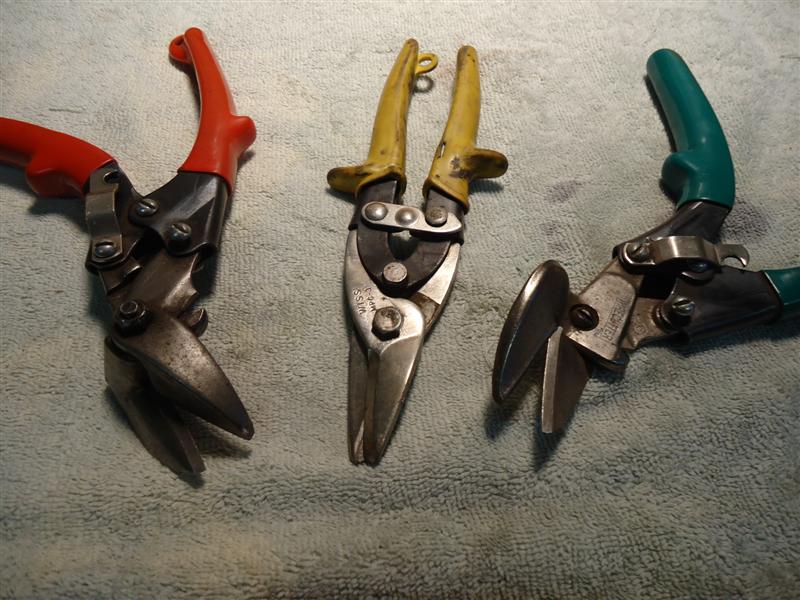
Read: 9 Ways To Cut Sheet Metal
Stop and check against the car for an exact fit. It's easy to remove metal - much more difficult to add it. You want to end up with a gap of no more than 1/8".
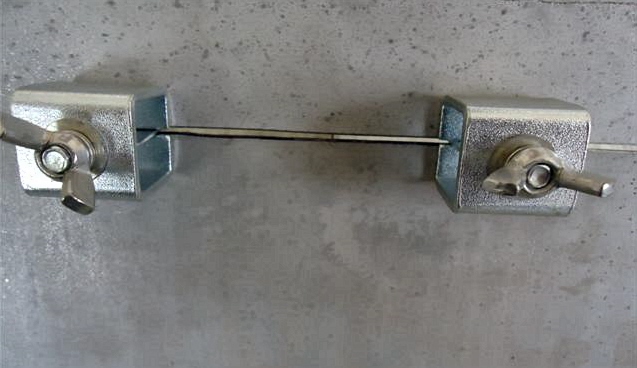
Welding new to old rusty metal is always tricky, especially after grinding the rust off old sections, which thins the metal even more. Burning through the old metal is always a concern.
Best Metal For Patch Panel
You can buy a new piece of sheet metal stock, or use an old piece of panel from a donor car, as long as it's grinded clean and of the same thickness.
How To Measure Sheet Metal Thickness
You can measure sheet metal thickness with a digital caliper or a sheet metal thickness gauge.
NOTE: Most classic American car body panels are 20 or 22 gauge. On pre-1970's cars, the width of the original sheet metal is often thicker (18 or 20 gauge).
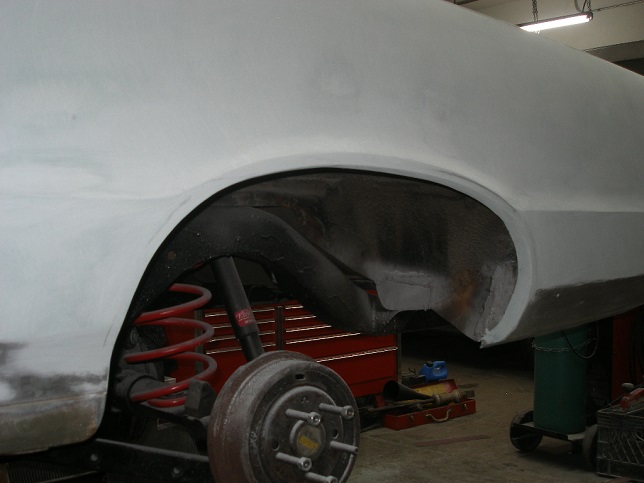
Curved Patch Panels
Patching into a curved area of the car body will take more time and skill than a simple flat patch. Before cutting out the old metal, study the damaged area and think through the repair process.
You may decide to remove the entire section to make the patch and welding more accessible. Cutting the panel bigger than the damaged area may give you a cleaner and easier butt weld.
***************************
Related Articles: